Improve Welding Performance: Invest in Dependable Inspection Service
Wiki Article
Unveiling the Diverse Variety Of Welding Services and Their Advantages
As markets continue to demand and evolve accuracy in their manufacturing procedures, the significance of welding solutions has ended up being increasingly pronounced. From the flexibility of arc welding to the performance of MIG welding, and the elaborate job achieved through TIG welding to the precision of laser welding, the selection of welding techniques offered is substantial.Kinds Of Welding Services
One common type is MIG welding, also understood as Gas Metal Arc Welding (GMAW), which makes use of a cord electrode to sign up with steels together. One more commonly utilized technique is TIG welding, or Gas Tungsten Arc Welding (GTAW), which utilizes a non-consumable tungsten electrode to create a clean and precise weld.Additionally, there is Stick welding, or Secured Steel Arc Welding (SMAW), which is recognized for its simpleness and performance, specifically in exterior or windy problems. This approach is frequently utilized in building and pipeline welding. Last but not least, there is Flux-Cored Arc Welding (FCAW), which is a versatile procedure appropriate for thick materials and can be used in both semi-automatic and automatic applications. Each kind of welding solution has its strengths and is picked based on aspects such as material kind, density, and the particular requirements of the task handy.
Advantages of Arc Welding
Arc welding uses a multitude of benefits that provide to various commercial requirements and demands. Furthermore, arc welding is known for its high welding rates, which can dramatically raise efficiency in manufacturing processes.An additional trick benefit of arc welding is its ability to produce sturdy and solid welds. The warmth produced throughout the process helps to develop a metallurgical bond in between the base metals, resulting in welds that have the ability to withstand high degrees of stress and anxiety and pressure. Arc welding also produces clean and precise welds, lowering the demand for added finishing work. On the whole, the benefits of arc welding make it a beneficial tool for numerous sectors wanting to attain high-quality welds effectively.
Advantages of MIG Welding
With a concentrate on effectiveness and sturdiness in welding procedures, MIG welding provides a distinctive collection of benefits that match the versatility and strength discovered in arc welding. MIG welding, or Gas Metal Arc Welding (GMAW), is understood for its speed and convenience of usage. The process involves feeding a cord electrode with a welding weapon, which is then thawed and used to sign up with the base products with each other. Among the key benefits of MIG welding is its high welding rates, making it a favored choice for jobs that call for quick turnaround times.In addition, MIG welding generates tidy welds with marginal splatter, lowering the requirement for considerable clean-up after the welding procedure. The flexibility of MIG welding enables welding a vast array of products, including light weight aluminum, stainless steel, and moderate steel. This flexibility makes MIG welding appropriate for various industries, from automotive to building and construction.
Moreover, MIG welding is recognized for its high deposition rates, implying even more product can be deposited in a shorter quantity of time compared to other welding processes. This leads to raised productivity and cost-effectiveness for jobs that need large volumes of welds. In general, the benefits of MIG welding make it a valuable strategy for attaining durable and reliable welds across various applications.
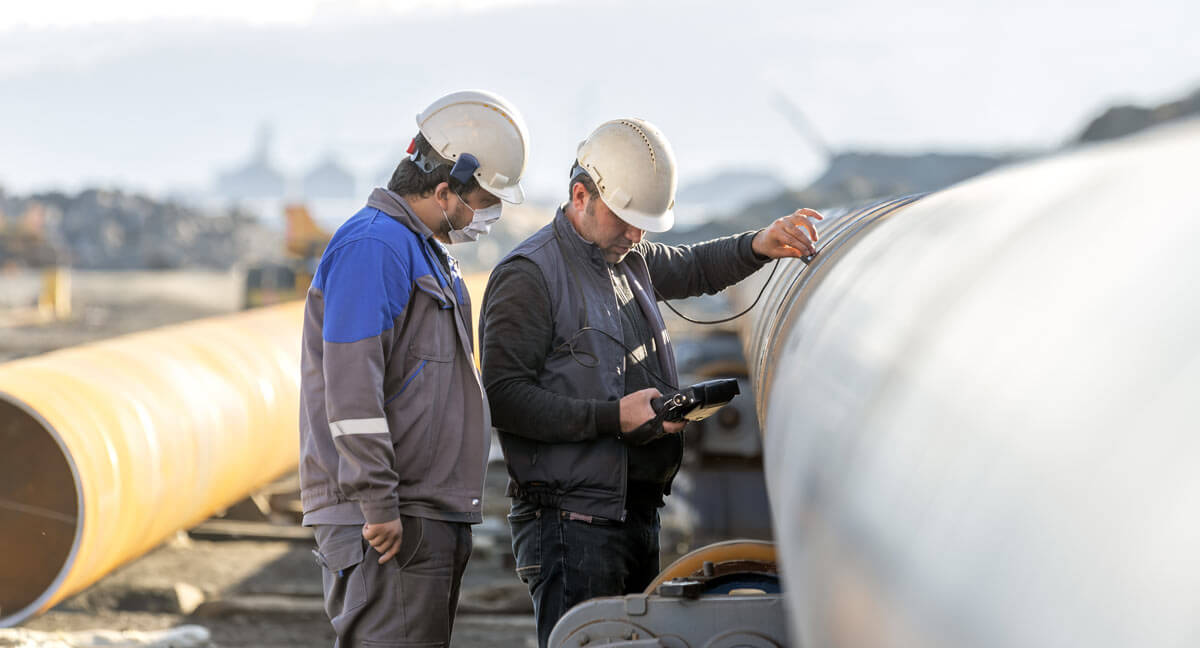
Exploring TIG Welding Advantages
TIG welding, likewise understood as Gas Tungsten Arc Welding (GTAW), provides a distinct set of benefits that accommodate accuracy and control in welding applications. One of the primary benefits of TIG welding is its ability to generate top notch, clean welds without the requirement for filler material. This makes it ideal for welding slim materials where aesthetics and accuracy are critical, such as in the aerospace and auto markets. In addition, TIG welding provides exceptional control over the warm input, causing very little distortion of the workpiece.In addition, TIG welding can be used on a vast variety of metals, consisting of stainless steel, light weight aluminum, titanium, and copper, making it a flexible selection for different welding tasks. The procedure also enables welding in different settings, supplying flexibility in challenging welding circumstances. TIG welding creates welds with remarkable strength and integrity, making it a preferred choice for vital applications where weld high quality is vital. On the whole, the accuracy, flexibility, and control offered by TIG welding make it a valuable technique in the welding industry (Welding Inspection Service).
Advantages of Laser Welding

An additional advantage of laser welding is its adaptability in working with a vast array of materials, including metals, plastics, and even dissimilar products. This flexibility Resources makes laser welding suitable for varied markets such as auto, aerospace, electronic devices, and medical devices. The non-contact nature of laser welding additionally lessens contamination, making it a eco pleasant and clean welding approach.
Furthermore, laser welding allows complicated and detailed weld geometries that might be challenging to achieve with typical welding techniques. This ability opens up new style opportunities and allows for the manufacturing of lighter and more innovative elements - Welding Inspection Service. Generally, the benefits of laser welding make it a recommended choice for several manufacturing applications seeking high accuracy and effectiveness
Verdict

Finally, the varied array of welding services use various advantages in various industries. Arc welding offers sturdy and strong welds, while MIG welding uses performance and flexibility. TIG welding makes sure specific and clean welds, and laser welding provides high precision and speed. Each sort of welding service has its own advantages and applications, accommodating various requirements and needs in the welding market.
From the flexibility of arc welding to the effectiveness of MIG welding, and the elaborate work completed through TIG welding to the accuracy of laser welding, the array of welding strategies readily available is substantial. One common kind is MIG welding, likewise understood as Gas Steel Arc Welding (GMAW), which makes use of a cable electrode to sign up with metals together. Additionally, arc welding is known for its high welding rates, which can substantially raise productivity in producing look at here now processes.With an emphasis on effectiveness Discover More and toughness in welding procedures, MIG welding presents a distinctive set of benefits that match the flexibility and strength located in arc welding.TIG welding, likewise known as Gas Tungsten Arc Welding (GTAW), offers a distinctive collection of benefits that provide to precision and control in welding applications.
Report this wiki page